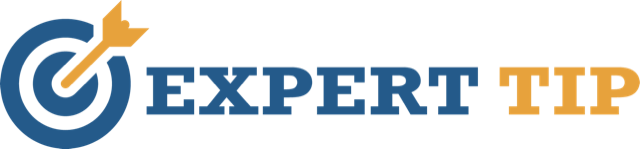
SPONSORED CONTENT
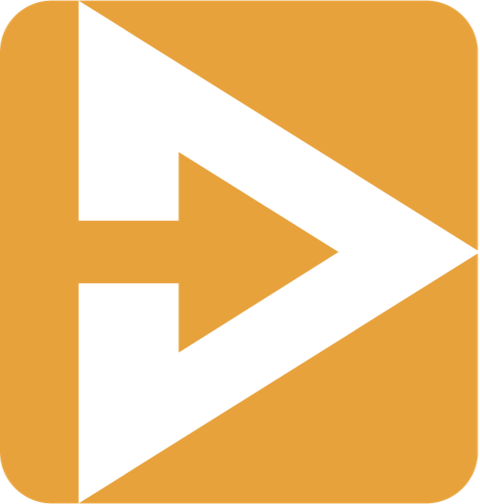
TIP: Ensure your 340B program has established ordering procedures and practices to optimize replenishment for maximum cost savings.
For optimal cost savings in your 340B program, it is critical to streamline the replenishment process using established ordering procedures. To get started, ensure that your 340B program maintains accurate and up-to-date information. This accurate program data is essential for managing accumulations, facilitating replenishments, and ensuring accurate ordering for qualified 340B claims.
Ordering for replenishment involves a few key aspects: proper operational setup, an understanding of which drugs can be ordered, and how to order them. First, it’s important to have a comprehensive understanding of which drugs can be automatically ordered via EDI setup. Many medications can be ordered by your system without the need for further intervention or additional information from the wholesaler.
Additionally, it’s crucial to be aware of drug replenishments that may require extra information, such as REMS, dropships, or specialty items. These specific medications will necessitate additional details like patient information, lab results, provider data, and more, which must be provided by the responsible ordering party.
Lastly, it’s essential to emphasize the importance of follow-up actions to complete the replenishment process, as items can sometimes be backordered, discontinued, or allocated for various reasons.
By thoroughly understanding your program’s overall ordering process and implementing effective follow-up procedures, your 340B program can successfully manage replenishments and maximize cost savings.
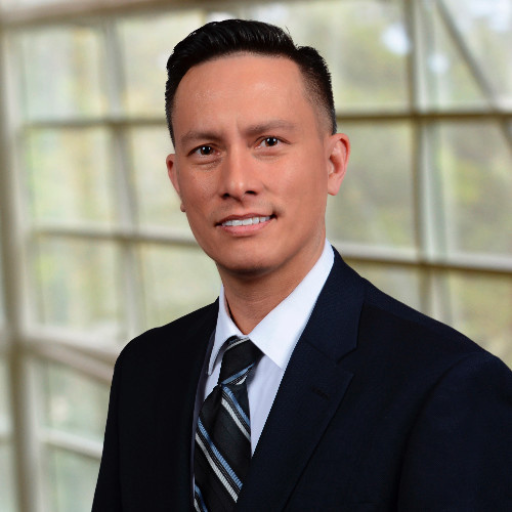
Paul Melland, senior director for client success, can be reached at pmelland@rxstrategies.com
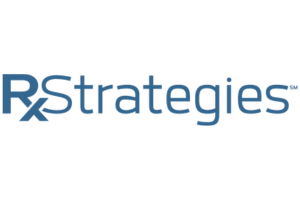